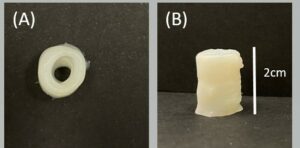
ABSTRACT
3D bioprinting has recently emerged as a crucial technology in tissue engineering, yet there are still challenges in selecting materials to obtain good print quality. Therefore, it is essential to study the influence of the chosen material (i.e., bioink) and the printing parameters on the final result. The “printability” of a bioink indicates its suitability for bioprinting. Hydrogels are a great choice because of their biocompatibility, but their printability is crucial for exploiting their properties and ensuring high printing accuracy. However, the printing settings are seldom addressed when printing hydrogels. In this context, this study explored the printability of double network (DN) hydrogels, from printing lines (1D structures) to lattices (2D structures) and 3D tubular structures, with a focus on printing accuracy. The DN hydrogel has two entangled cross-linked networks and a balanced mechanical performance combining high strength, toughness, and biocompatibility. The combination of Poly(ethylene glycol)-diacrylate (PEDGA) and Sodium Alginate (SA) enables the qualities mentioned above to be met, as well as the use of UV to prevent filament collapse under gravity. Critical correlations between the printability and settings, such as velocity and viscosity of the ink, were identified. PEGDA/alginate-based double network hydrogels were explored and prepared, and printing conditions were improved to achieve 3D complex architectures, such as tubular structures. The DN solution ink was found to be unsuitable for extrudability; hence, glycerol was added to enhance the process.
MATERIALS
- Regemat 3D BioV1
- Sodium alginate
- Poly(ethylene glycol)-diacrylate (PEDGA) (average Mn700)
- Calcium chloride
- Glycerol 99%
- Igracure 2959 (2-Hydroxy-4’-(2-hydroxyethoxy)-2-methylpropiophenone)
METHOD
PEGDA was first dissolved in distilled water at 40 % (w/v) concentration, and the photoinitiator I2959 was added to the PEGDA precursor solution at 1 % (w/v) concentration. After that, a double network solution was obtained, adding 4% (w/v) of SA. Different glycerol concentrations were tested to study the influence of the viscosity on the printing process, but the best in terms of printability and shape fidelity is 25%. All the solutions, before the cross-linking, were stirred until they became homogeneous and degassed for 2h to eliminate air bubbles. The solutions were then polymerized by ultraviolet (UV wavelength 365nm) irradiation during the printing process. Then, the obtained hydrogels were transferred into the CaCl2 solution for 5h to achieve the crosslinking of alginate. The purpose of choosing this approach is to avoid the filament from collapsing during the printing process.
BIOPRINTING PARAMETERS
Several flow speed and different distances between the needle and the plate have been tested. The best results are given by a flow speed of 2mm/s and height of 0.340mm
REFERENCE
Greco, Immacolata, Vanja Miskovic, Carolina Varon, Chiara Marraffa, and Carlo S. Iorio. “Printability of Double Network Alginate-Based Hydrogel for 3D Bio-Printed Complex Structures.” Frontiers in Bioengineering and Biotechnology 10 (2022).
Number | Category | Product | Amount |
---|
One thought on “Printability of Double Network Alginate-Based Hydrogel for 3D Bio-Printed Complex Tubular Structures”
very interesting biomaterial!