Introduction
Electrically conductive thermoplastic elastomers hold idyllic attributes for the 3D printing of flexible and electroconductive scaffolds with applications in electronics, electromagnetics and computer industries. Beyond these applications, they have a tremendous potential in the biomedical sector. Due to their enhanced biocompatibility, they can be used as biosensors and have a great potential in the engineering of tissues and organs receiving mechanical and electrical signals, such as the musculoskeletal and nervous systems. Once the scaffolds are printed, cells can be directly added to the surface of the scaffold or embedded in a hydrogel that can be injected into the pores of the scaffold. After 3D printing, the 3D constructs can be electrically and mechanically stimulated to determine the effects of these stimuli on cell behavior (i.e. cell proliferation, cell migration, cell differentiation, etc.) through biomimicry. The Electroflex filament employed in this protocol is supplied as a thermoplastic filament, the most common material in the 3D printing community, and is 100% compatible with the filament extruder of REGEMAT 3D bioprinting systems. The following protocol describes a method for generating scaffolds with high resolution and reproducibility.
Materials
- Electroflex filament
Equipment required
- REGEMAT 3D Bio V1 bioprinter with filament extruder
- PC with REGEMAT 3D Designer software
Methods
- Turn on the bioprinter, connect it to the PC and launch REGEMAT 3D Designer software. Click “Connect” button.
- Select “Titan Extruder” in the header configuration and proceed with its calibration.
- Load the biomaterial in the filament extruder head.
- Heat the nozzle at the melting temperature of the material which in this case is 250°C.
- Load the .stl file with the 3D design of the desired 3D structure to print, select extra and object configurations and proceed to print on the glass bed.
Recommendations of extra an object configuration
It is recommended to set an infill speed of 4 mm/s, a travel speed of 20 mm/s and a retract speed of 30 mm/s. The retract traveling works properly at 2 units.
According to the object configuration, this is a practical example:
Scaffold | Cylinder |
Layer height (mm) | 0.26 |
Total layers | 39 |
Size (mm) | 10 x 10 (h x d) |
Pore size (mm) | 1 x 1 |
Infill pattern | Diagonal, with 90° angle |
Temperature (°C) | 250 |
Flow speed (mm/s) | 1.25 |
Clarifications
- This protocol has been tested using a 0.8 mm nozzle, therefore the use of another nozzle could imply the change of some parameters.
- So as to obtain a higher adherence of the material to the bed it is advisable to switch off the layer fan and heat the bed temperature up to 60°C
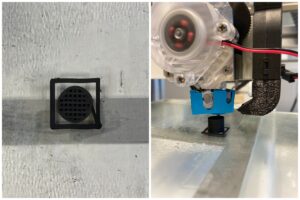
Number | Category | Product | Amount |
---|---|---|---|
1 | - | Electroflex Filament | 1 |